Printed nylon rugs have become a staple in both residential and commercial spaces, offering durability, vibrant designs, and ease of maintenance. Understanding the manufacturing process behind these rugs provides insight into their quality and longevity.
The journey of a printed nylon rug begins with the selection of high-quality nylon fibers, chosen for their resilience and dye affinity. Designers then employ advanced software to create intricate patterns, ensuring precision and scalability. These designs are brought to life through printing technologies such as inkjet and screen printing, each offering unique benefits in terms of color vibrancy and production efficiency.
Post-printing, rugs undergo finishing processes to enhance their appearance and durability, including heat setting and chemical treatments. Rigorous quality control measures are implemented to ensure each rug meets established standards. Manufacturers are also increasingly adopting sustainable practices, utilizing recycled materials and eco-friendly dyes to minimize environmental impact.
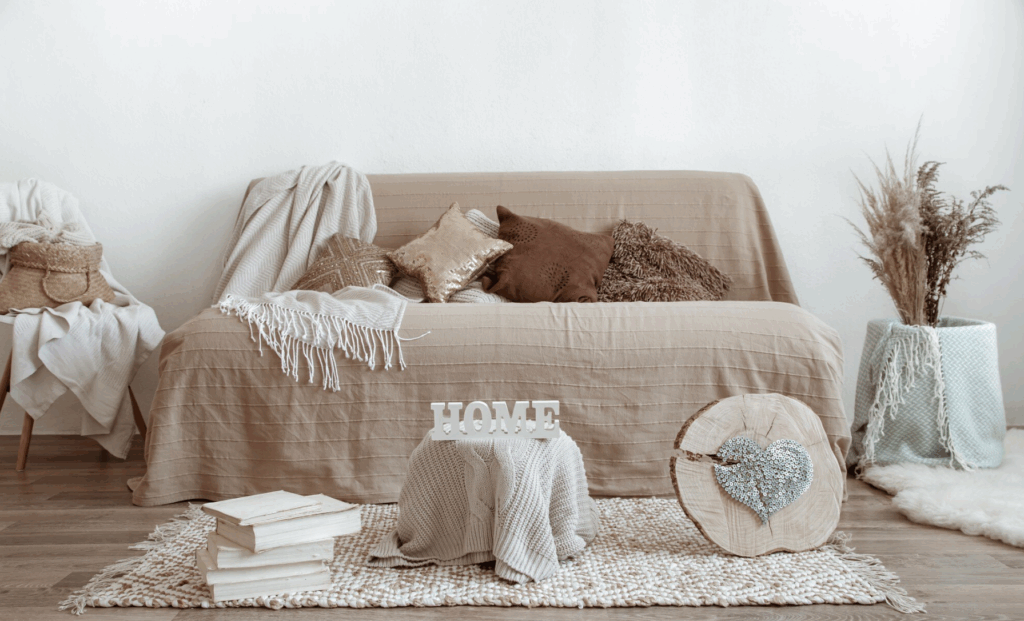
Why Nylon? The Science Behind Fiber
Nylon stands as a cornerstone in the realm of synthetic fibers, particularly in the manufacturing of printed rugs. Its unique combination of strength, resilience, and versatility makes it an ideal choice for both residential and commercial applications.
Key Features of Nylon
- Molecular Structure and Strength: At the heart of nylon’s durability lies its molecular architecture. Nylon is a polyamide, characterized by repeating units linked by amide bonds. These bonds facilitate strong hydrogen bonding between polymer chains, resulting in a material that boasts high tensile strength and resistance to abrasion. This structural integrity ensures that nylon fibers can withstand significant stress without deforming, making them suitable for high-traffic areas.
- Resilience and Elasticity: One of nylon’s standout properties is its exceptional resilience. The fiber’s ability to stretch and recover allows it to maintain its shape and appearance over time. This elasticity is particularly beneficial in rug applications, where fibers are subjected to constant foot traffic and pressure. Nylon’s resilience ensures that rugs retain their texture and form, even under heavy use.
- Dye Affinity and Color Retention: Nylon’s chemical composition grants it a strong affinity for dyes, enabling vibrant and long-lasting coloration. The property is crucial for printed rugs, where intricate designs and color fidelity are paramount. Additionally, nylon’s resistance to fading ensures that these colors remain vivid over time, even when exposed to sunlight and cleaning agents.
- Stain Resistance and Maintenance: Modern nylon fibers are often treated with stain-resistant finishes, enhancing their ability to repel spills and dirt. The treatment simplifies maintenance, allowing for easy cleaning and prolonging the rug’s aesthetic appeal. The combination of inherent stain resistance and ease of maintenance makes nylon rugs a practical choice for households and commercial spaces alike.
- Environmental Considerations: Advancements in nylon production have led to the development of more sustainable variants, such as nylon 6, which can be recycled more efficiently than its counterparts. This recyclability reduces environmental impact and aligns with growing consumer demand for eco-friendly products.
From Concept to Design: Where Art Meets Algorithm
The creation of printed nylon rugs is a harmonious blend of artistic vision and technological precision. This process begins with conceptualizing designs that resonate with aesthetic appeal and functional requirements. Designers employ advanced software tools to translate their creative ideas into detailed digital patterns, ensuring accuracy and scalability.
Digital Design Tools
Modern rug design leverages specialized software platforms that offer a suite of features tailored for textile applications. These tools facilitate intricate pattern creation, color management, and realistic simulations, enabling designers to visualize the final product before production. Such software ensures that the designs are not only visually compelling but also technically feasible for manufacturing.
Integration of Algorithmic Design
Algorithmic design introduces computational methods into the creative process, allowing for the generation of complex patterns through mathematical algorithms. This approach enables designers to explore a vast array of design variations efficiently, fostering innovation and uniqueness in rug patterns. By adjusting parameters within the algorithms, designers can achieve precise control over the design elements, ensuring consistency and originality.
AI-Driven Creativity
Artificial Intelligence (AI) is increasingly playing a pivotal role in textile design. AI-powered platforms analyze extensive datasets, including market trends and consumer preferences, to generate design suggestions that align with current demands. These systems can produce numerous unique patterns rapidly, enhancing the speed and diversity of the design process. Moreover, AI ensures a high degree of originality in designs, often incorporating mechanisms to certify uniqueness and prevent duplication.
From Digital Concept to Physical Product
Once a design is finalized digitally, it undergoes a series of preparations for printing. This includes color calibration to match the digital hues with physical dyes and adjusting the design to accommodate the specific dimensions and characteristics of the nylon rug. The seamless transition from digital design to physical product is facilitated by the compatibility of design software with printing technologies, ensuring fidelity and quality in the final rug.
Printing Technologies Unveiled: Inkjet vs. Screen Printing
In the realm of printed nylon rugs, two primary printing technologies stand out: inkjet printing and screen printing. Each method offers distinct advantages and considerations, influencing factors such as design complexity, production volume, and cost.
Inkjet Printing: Precision and Flexibility
Inkjet printing, a digital process, involves spraying tiny droplets of ink directly onto the nylon substrate. This method excels in producing intricate designs with high-resolution details.
Advantages:
- Design Versatility: Inkjet printing allows for unlimited design variations without the need for physical screens. This flexibility is ideal for custom or short-run productions.
- Quick Turnaround: Digital files can be printed directly, reducing setup time and enabling faster production cycles.
- Efficient for Small Batches: Without the need for screen preparation, inkjet printing is cost-effective for low-volume orders.
Considerations:
- Ink Compatibility: The inks used must be compatible with nylon fibers to ensure proper adhesion and color vibrancy.
- Durability: While advancements have been made, inkjet prints may require additional treatments to match the durability of screen-printed counterparts.
Screen Printing: Vibrancy and Longevity
Screen printing involves creating a stencil (or screen) for each color in the design, through which ink is applied onto the rug. This traditional method is renowned for producing vivid and long-lasting prints.
Advantages:
- Color Intensity: The technique allows for the application of thick ink layers, resulting in vibrant and opaque colors.
- Durability: Screen-printed designs are known for their resistance to wear and repeated cleaning, making them suitable for high-traffic areas.
- Cost-Effective for Large Runs: Once screens are prepared, the per-unit cost decreases significantly with higher production volumes.
Considerations:
- Setup Time: Creating screens for each color can be time-consuming, making it less efficient for small orders.
- Design Limitations: Complex, multi-colored designs may require multiple screens, increasing production complexity and time.
Choosing the Right Method
The decision between inkjet and screen printing hinges on specific project requirements:
- For intricate, multi-colored designs or small batches, inkjet printing offers flexibility and speed.
- For bold, long-lasting designs in large quantities, screen printing provides cost-effectiveness and durability.
Understanding the nuances of each method ensures that the final product aligns with both aesthetic and functional expectations.
The Finishing Touches: Locking in Color and Texture
The final stages of manufacturing printed nylon rugs are crucial in enhancing their appearance, durability, and overall quality. These finishing processes—heat setting, chemical treatments, shearing, and binding—ensure that each rug not only looks appealing but also withstands the rigors of daily use.
Heat Setting: Stabilizing Fiber Structure
Heat setting is a thermal process that stabilizes the molecular structure of nylon fibers, locking in the twist and shape imparted during yarn formation. This process enhances the rug’s dimensional stability, resilience, and appearance retention.
Two primary methods are employed:
- Suessen Process: Utilizes dry heat at temperatures exceeding 425°F (218°C) to set the yarns.
- Superba Process: Employs saturated steam at lower temperatures, offering a gentler treatment that reduces the risk of fiber degradation.
Heat setting not only improves the rug’s texture and appearance but also enhances its resistance to crushing and matting, ensuring longevity.
Chemical Treatments: Enhancing Performance
Post-printing, rugs undergo chemical treatments to bolster their functional properties:
- Stain Resistance: Application of fluorochemical agents creates a barrier that repels liquids and prevents stains from setting.
- Colorfastness: Fixatives are used to bind dyes to the fibers, reducing the likelihood of color fading due to washing or exposure to light.
- Antimicrobial Finishes: These inhibit the growth of bacteria and mold, contributing to a healthier indoor environment.
These treatments are essential in maintaining the rug’s aesthetic appeal and ensuring it meets performance standards.
Shearing: Achieving Uniform Texture
Shearing involves trimming the rug’s surface to a uniform height, enhancing its texture and clarity of design. This process removes any irregularities or loose fibers, resulting in a smooth and even pile. Shearing is particularly important for revealing intricate patterns and ensuring a consistent feel underfoot.
Binding: Securing and Finishing Edges
Binding is the process of reinforcing the rug’s edges to prevent fraying and add a polished finish:
- Standard Binding: Involves sewing a fabric tape around the rug’s perimeter, providing durability and a clean edge.
- Serging: A continuous overlock stitch is applied, wrapping yarn around the edge for a more traditional look.
- Fringing: Decorative tassels are added to the ends, often seen in more traditional or oriental rug designs.
The choice of binding method affects both the rug’s durability and its aesthetic, allowing customization to suit various interior styles.
Rigorous Quality Control: The Unsung Hero
Quality control is a critical component in the manufacturing of printed nylon rugs, ensuring that each product meets the highest standards of durability, appearance, and performance. This meticulous process involves multiple stages, each designed to identify and rectify potential issues before the rugs reach consumers.
Visual Inspection: The First Line of Defense
The quality assurance journey begins with a thorough visual inspection. Skilled inspectors examine each rug for surface defects such as:
- Color inconsistencies: Ensuring uniformity across the rug.
- Printing errors: Checking for misalignments or smudges in the design.
- Physical imperfections: Identifying frayed edges, loose threads, or uneven pile.
This step is crucial in maintaining the aesthetic appeal and structural integrity of the rugs.
Performance Testing: Ensuring Durability
Beyond visual assessments, rugs undergo rigorous performance testing to simulate real-world usage:
- Abrasion resistance: Evaluating how well the rug withstands wear from foot traffic.
- Colorfastness: Testing the rug’s ability to retain color when exposed to light, washing, and rubbing.
- Tensile strength: Measuring the force required to tear the rug, ensuring it can endure daily use.
These tests help in predicting the rug’s longevity and performance in various environments.
Dimensional Accuracy: Precision Matters
Ensuring that each rug meets specified dimensions is vital, especially for custom orders or installations:
- Size verification: Confirming length and width match the design specifications.
- Shape consistency: Checking for distortions or warping that could affect placement.
Accurate dimensions are essential for customer satisfaction and seamless integration into spaces.
Edge Finishing and Binding: Securing the Structure
The edges of the rug are inspected to ensure proper finishing techniques have been applied:
- Binding integrity: Ensuring the edges are securely stitched to prevent unraveling.
- Uniformity: Checking that the binding is consistent in width and color, complementing the rug’s design.
Proper edge finishing enhances both the durability and visual appeal of the rug.
Documentation and Traceability: Maintaining Standards
Comprehensive records are maintained throughout the quality control process:
- Inspection reports: Detailing findings at each stage of the quality check.
- Corrective actions: Documenting any issues found and the steps taken to address them.
- Batch tracking: Assigning unique identifiers to each production batch for traceability.
This documentation ensures accountability and facilitates continuous improvement in manufacturing practices.
Sustainability: Balancing Aesthetics and Ethics
Sustainability in the manufacturing of printed nylon rugs is increasingly becoming a focal point for both producers and consumers. As environmental concerns rise, the industry is adopting practices that balance aesthetic appeal with ethical responsibility.
Embracing Recycled Nylon: The Rise of ECONYL®
Traditional nylon production is energy-intensive and relies heavily on fossil fuels, contributing significantly to environmental degradation. In response, manufacturers are turning to recycled nylon alternatives like ECONYL®. Developed by Aquafil, ECONYL® is regenerated nylon made from waste materials such as discarded fishing nets, fabric scraps, and old carpets. This closed-loop process not only reduces waste but also cuts carbon emissions by up to 90% compared to conventional nylon production.
By incorporating ECONYL® into rug manufacturing, companies are producing high-quality products that meet consumer demands for sustainability without compromising on performance or design.
Eco-Friendly Dyeing and Finishing Processes
The dyeing and finishing stages of rug production traditionally involve chemicals that can be harmful to the environment. To mitigate this, manufacturers are adopting low-impact and plant-based dyes, which reduce water pollution and energy consumption. Additionally, advancements in dyeing technology, such as non-aqueous dye baths, are being explored to further minimize environmental impact.
These eco-friendly practices ensure that the vibrant colors and textures of printed nylon rugs are achieved without compromising environmental integrity.
Implementing Circular Economy Principles
The concept of a circular economy is gaining traction in rug manufacturing, emphasizing the reuse and recycling of materials to extend product life cycles. Companies like FLOR are leading the way by designing rugs that can be disassembled and recycled at the end of their use. Their partnership with Aquafil to use ECONYL® yarns exemplifies this commitment to sustainability.
Such initiatives not only reduce landfill waste but also conserve resources, aligning with broader environmental goals.
Certifications and Consumer Transparency
To assure consumers of their commitment to sustainability, manufacturers are obtaining certifications from recognized organizations. Labels such as OEKO-TEX® Standard 100, GOTS (Global Organic Textile Standard), and Cradle to Cradle Certified™ indicate that products meet stringent environmental and social criteria.
The Path Forward: Sustainable Innovation
The journey toward sustainable printed nylon rugs is ongoing, with continuous innovation driving progress. Research into bio-based nylons derived from renewable resources like plant sugars is underway, promising to further reduce reliance on fossil fuels.
Maintenance Tips for Printed Nylon Rugs
Maintaining the beauty and longevity of your printed nylon rug requires a combination of regular care and prompt attention to spills and stains. Nylon’s inherent durability and stain resistance make it a popular choice for both residential and commercial settings, but to keep it looking its best, consider the following maintenance tips:
Regular Vacuuming: Your First Line of Defense
Regular vacuuming is essential to remove dirt and debris that can wear down the fibers of your nylon rug. Aim to vacuum at least once a week, and more frequently in high-traffic areas. Use a vacuum cleaner with a rotating brush or beater bar to effectively lift dirt from the rug’s surface. However, ensure that the vacuum’s settings are appropriate for your rug to avoid damaging the fibers.
Immediate Spill Response: Act Fast
Promptly addressing spills can prevent stains from setting into your nylon rug. Blot the spill with a clean, white cloth or paper towel to absorb as much liquid as possible. Avoid rubbing, as this can spread the stain and damage the fibers. For most spills, a solution of mild dish soap and warm water can be effective. Apply the solution to the stained area, blot gently, and rinse with clean water. Always test any cleaning solution on an inconspicuous area first to ensure it doesn’t affect the rug’s color.
Deep Cleaning: Periodic Refresh
Even with regular vacuuming, your nylon rug will benefit from periodic deep cleaning to remove embedded dirt and refresh the fibers. It’s recommended to have your rug professionally cleaned every 12 to 18 months, depending on usage. Professional cleaning methods, such as hot water extraction, can effectively remove deep-seated dirt without damaging the rug.
Protective Measures: Extend Your Rug’s Life
Implementing protective measures can help maintain your nylon rug’s appearance:
- Use Rug Pads: Placing a rug pad underneath can prevent slipping, provide additional cushioning, and reduce wear.
- Rotate Regularly: Rotating your rug every few months ensures even wear and exposure to sunlight, preventing uneven fading and wear patterns.
- Limit Sun Exposure: Prolonged exposure to direct sunlight can cause colors to fade. Use window treatments to limit UV exposure or rotate the rug periodically.
Stain Protection Treatments: Added Defense
Consider applying a fabric protector specifically designed for nylon rugs. These treatments can add an extra layer of defense against stains and make cleaning spills easier. Be sure to follow the manufacturer’s instructions and test the product on a small area first.
Conclusion
The journey of a printed nylon rug from concept to final product involves a blend of science, art, and meticulous craftsmanship. By understanding this process, consumers can appreciate the quality and value embedded in each rug.
FAQs
Q1: Are printed nylon rugs suitable for high-traffic areas?
Yes, their durability makes them ideal for areas with heavy foot traffic.
Q2: Can I use a printed nylon rug outdoors?
While some are designed for outdoor use, always check the manufacturer’s specifications.
Q3: How often should I clean my nylon rug?
Regular vacuuming is recommended, with professional cleaning annually or as needed.
Q4: Do printed nylon rugs fade over time?
With proper care and limited sun exposure, they maintain their color for years.
Q5: Are these rugs eco-friendly?
Many manufacturers now employ sustainable practices, but it’s best to verify specific product details.